
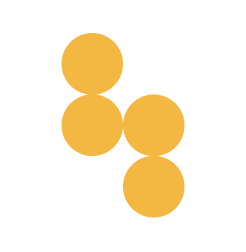
SUSTAINABILITY REPORT
Tempo Scan’s ("the Company") support to the Sustainable Development Goals (SDGs) has been carried out through various program and initiatives integrated with policies and procedures relevant with industry sector where the Company operates. The initiatives are as explained hereunder.
SDG Goal 1: No Poverty
The Company’s CSR targeted to underprivileged community is program to support Indonesian Children becoming #SiapJadiKuatdanCerdas.
vidoran shares goodness by giving vidoran Xmart 1+ Growing Up Milk with a total value of Rp 6,7 Billion to more than 20,000 children of Orphans, Schools and Government Institution in Indonesia. vidoran Xmart has been trusted by 9 out of 10 Indonesian mothers because of the nutritional composition in the complete imunUp formula. Furthermore, vidoran Xmart is also a healthier choice for Indonesian children with lower sugar content, high DHA, inulin, vitamin C, D3, E, and Zinc to support nutritional fulfilment in order to create intelligent Indonesian children with strong body immune and optimal growth.
SDG Goal 2: Zero Hunger
In 2023, bodrex once again introduced a CSR program during the Ramadan period, titled #bodrexMerahPutihBerbagi Berkah Ramadan. This CSR program aims to provide nutritious iftar meal packages to those in need, enabling them to maintain their daily activities and enjoy their fasting days. bodrex distributed 1,500 iftar meal packages to others through a Food Truck that travelled to various locations in Jabodetabek.
SDG Goal 3: Healthy Life and Well-being
In 2023, S.O.S raised the message of the importance of keeping clean for healthy and comfortable living through S.O.S Squad campaign with the theme "Clean Home, Comfortable Family". In this CSR activity, S.O.S reached 200 orphanages and nursing homes in more than 20 cities across Indonesia by providing donations in the form of Home Care hygiene products and other Tempo Scan products with total donation of more than Rp 1.8 Billion as well as carrying out clean-up activities.
SDG Goal 4: Quality Education
The Company is continuously implemented the training program designed to all employee in order to meet demands of increasingly complex tasks or assignments planned and executed in regularly basis throughout the year. The training program includes technical training according to employee work functions, managerial and leadership training and other topics.
The Company also continues the training program called Management Trainee (MT) program is designed to fresh graduates joining the Company. The program is aimed these fresh graduates to comprehend the business process as a whole.
The Company also provides certification training in accordance to applicable regulations for employees who carry out certain tasks that require certain certifications, among others certifications related to Work Safety and Health and the environment (K3L) and product quality, Fire Fighter certification, Halal certification and certain Machinery Operator certification.
SDG Goal 5: Gender equality
Support and implementation of gender equality in the Company is reflected in the representation of the composition of the number of women employees that are equivalent with the number of men employees.
SDG Goal 6: Clean Water and Sanitation
The core of the water conservation program is water management for the production process and for factory household needs which is carried out in accordance with the 3R principle (Reduce, Reuse and Recycle).
The first R, namely Reducing water consumption, is carried out through various efforts such as keeping water pipes from leaking, perfecting procedures for cleaning production equipment during cleaning in place (CIP) or during off-line cleaning (COP) to make it more economical. water without compromising the level of cleaning effectiveness. Adjustments are made with a systematic approach, such as adjusting the CIP computer program, establishing, and testing enhanced cleaning standard operating procedures (SOP) and validating before new cleaning procedures are implemented effectively. Reducing water consumption is also influenced by employee behaviour, for further training and awareness through water saving campaigns for all employees as well has been carried out routinely.
The second R, namely Reusing water, have been done by adjusting the washing SOP in the production machine, the water resulting from the final rinsing (final stage) of a CIP that is still clean can be used to carry out the pre-rinsing stage (first stage) in the next CIP.
The third R, namely Recycling water. Liquid waste from cleaning in the production process or from domestic use is channelled to the waste water treatment plant (IPAL) for separation of water waste and solid waste in accordance with applicable regulations. The Manufacturing Division has initiated to further processing the wastewater resulting from IPAL waste processing for meeting the recycling water standards for gardening purposes.
Moreover, Tempo Scan has implemented the construction of infiltration wells at the factories and start the rainwater harvesting program as part of the water conservation purposes.
To strengthen the commitment to water conservation, the water consumption target is set as one of the factory operational KPIs, where the target must be stricter from year to year to encourage continuous improvement.
SDG Goal 7: Affordable and Clean Energy
The Company continuously makes improvements in optimizing energy consumption to produce energy consumption that is more efficient in quantity.
Energy is an important element in the production process and other supporting activities at each of our factory locations. Currently electricity, gas fuel and diesel fuel are energy sources used in operations of manufacturing facilities. In realizing the company’s responsibility to the environment, the principle of utilizing energy is to use it as efficiently as possible and make energy sources with the lowest levels of CO2 emissions a priority and start utilizing renewable energy.
The source of electrical energy for some of our factories is supplied by PLN and others are supplied by private electricity companies which predominantly use natural gas, which is more environmentally friendly than coal and diesel. Meanwhile, diesel fuel is used for steam generating engines which have now been massively replaced by steam generating engines using natural gas. The conversion process from diesel to gas has been completed for all factories in PMG (Pharmaceutical Manufacturing Group) and ini grup BNMG (Beverage & Nutrition Manufacturing Group).
Our steps to implement renewable energy have also begun, with the Manufacturing division has started using solar cell panels (Solar PV) for preheating boiler feed water as a pilot project. In line with the increasingly affordable price of solar cells, the company is exploring the application of these solar cells in all factories in the Manufacturing division as a source of electrical power for factories through a hybrid system with the existing electricity supply.
The next real step in ensuring energy conservation is to save on usage or carry out efficient energy consumption. Energy saving efforts at each factory location are measured and monitored every day as part of the factory management key performance indicators (KPI). The targets in KPI are determined based on the principle of continuous improvement and must be better from year to year.
Activities to save energy begin with creating awareness among all employees about saving energy usage. Efficient energy use is directly related to the efficiency of the production line which is reflected in Overall Equipment Efficiency (OEE). Efforts to improve OEE, such as improving equipment conditions, have an impact on significantly increasing OEE at all factory locations, which means that production volumes at certain levels can be carried out with fewer resources. The Manufacturing division has also launched a policy in purchasing new machines, so that a more efficient level of energy use is one of the considerations in making decisions about which type of machine to buy.
For existing production facilities, the focus is on carrying out corrective actions that make it possible to make these facilities more efficient in energy use, including stopping energy waste through leaks in installations and production equipment.
In steam power system, the condensate produced from the process of using steam power, which still contains a lot of heat energy, has been used to utilize the heat using a recovery system. Condensate from steam power is returned to the boiler system for pre-heating of the boiler feed water which has room temperature and this can also reduce the fresh water needed as feed water for the boiler itself. Apart from that, technical studies of the installation of steam power systems required for the production process of a factory have also resulted in the opportunity to adapt lower and optimal steam pressures to the needs of production equipment and contribute to reducing heating energy needs.
The compressed air supply system is also a major user of electrical energy. Repairing the air pressure system, by overcoming leaks and adjusting the pressure to an optimal level so that the air compressor system does not work too often is an effort to save electrical energy.
Apart from that, in the field of HVAC (Heating, Ventilation & Air Conditioning) systems, improvements were made : by changing the cooling system which originally used an air-cooled chiller to a water-cooled chiller; use of thermal storage tanks so that HVAC cooling performance becomes more efficient; as well as optimizing and balancing air pressure between rooms through the Building Automation System (BAS) which automatically controls and regulates the temperature and humidity in the production building.
The replacement of conventional electric motors with new motors equipped with frequency converters has begun gradually, allowing a further reduction in electricity consumption. Likewise for lighting lamps, the replacement of tube lamps (TL) with light emitting diodes (LED) is carried out in stages.
In terms of mindset and behaviour, the energy saving campaign continues to be carried out widely, reaching all employees to behave energysavingly in the factory also in their home.
SDG Goal 8: Decent Work and Economic Growth
The Company has provided decent work and income for its 4.540 employees throughout Indonesia and has participated in contributing to Indonesia’s economic growth as reflected in the Company’s impressive 2023 financial performance achievement.
The Company’s concern for the surrounding community in terms of empowering community resources, among others, by employing local workers for activities in the factory and branch office areas and handing over non-B3 waste processing activities to cooperatives or communities around the Company industry. In addition, The Company also empowers Small – Medium Enterprises (UMKM) as suppliers of goods and services within the Company while still adhering the implementation of good corporate governance.
In addition, the Company also contributes to the people’s economy through its Distribution division, where this division works together with traders and retailers to reach the consumers throughout Indonesia including the second and third tier cities outside provincial capitals. These traders and retailers mostly are small and medium enterprises (UMKM).
SDG Goal 9: Industry, Innovation, and Infrastructure
The Company, especially the Manufacturing division, consistently operates in accordance with Good Manufacturing Practices (GMP) standards, other Quality Management Systems such as ISO standards and regulations regarding product quality issued by authorities. As part of the ongoing process, the Company, namely Pharma Manufacturing Group, has once again obtained CPOTB (Cara Pembuatan Obat Tradisional yang Baik) certification for several dosage forms, CPOB (Cara Pembuatan Obat yang Baik) recertification for several production lines and ISO22000 implementation for product lines. export oriented. Meanwhile, the Consumer Products & Cosmetics Manufacturing Group consistently maintains CPKB (Cara Pembuatan Kosmetik yang Baik) certification from BPOM, CPPKRTB (Cara Pembuatan Perbekalan Kesehatan Rumah Tangga yang Baik) from the Ministry of Health and also SJH (Sistem Jaminan Halal). Meanwhile, the Beverage & Nutritional Manufacturing Group has obtained a CPPOB Certificate (Cara Produksi Pangan Olahan yang Baik) from BPOM for its Beverage Factory Facilities and has carried out a PMR Audit at the Intermediate Raw Material Factory for Powdered Milk Products.
In the Distribution division, to meet regulatory requirements, the Distribution division continues to maintain CDOB (Cara Distribusi Obat yang Baik) certification from the Indonesian Food and Drug Supervisory Agency (BPOM) with 51 CDOB certificates for non-Cold Chain Product (Non-CCP) pharmaceutical products and 38 CDOB certificates for CCP pharmaceutical products that have been applied for and approved during 2023.
Apart from that, infrastructure development to support business growth is also continuing, including increasing production and distribution capacity.
SDG Goal 10: Reduce Inequalities
The Company is open to anyone in recruiting prospective employees on an equal basis. The acceptance is based on skill and competency evaluation result and it has to match with the job requirement regardless of gender, ethnic, religion, social status or physical conditions, since the Company believes that human beings are created equal; therefore, they should have an equal access to job opportunities without any discrimination.
The Company does not have specific policies regarding the recruitment of local manpower. However, the Company keep prioritizing to recruit employees from the local areas as long as they meet the requirements and specifications.
SDG Goal 12: Responsible Consumption and Production
We design products with good quality products with high benefits and are produced by following the principles of Good Manufacturing Practices (GMP). Products with good quality are produced from a good and reliable manufacturing system, where to guarantee the reliability of the manufacturing unit in producing products with good quality, our factory besides ensuring the implementation of GMP principles also ensures good raw materials, reliable equipment and a quality control system strict production.
To ensure the accuracy of our products reaching the market, we also strengthen the company’s supply chain system, including production planning and material supply scheduling, which is carried out by the PPIC (Production Planning Inventory Control) team with the SAP system.
The number of consumer complaints is an indicator of the success of quality management in product design, materials, manufacturing processes and distribution processes for our products. The Manufacturing division makes the number of consumer complaints related to the manufacturing process one of the important parameters for internal factory improvements.
SDG Goal 13: Climate Action
As the Company’s commitment to reduce waste and pollution, the Company has implemented an operational system that reduces paper usage, among other in the process of order taking from its customers, the process is using paperless ordering system that use mobile application, where the orders are submitted by the sales team into this application called TiMOS and thereafter the orders are processed directly into the computer system at the head office which is directly connected to the company’s warehouses for further processing. Apart from that, the Tempo Direct® Application has been developed which is aimed at customer partners, where this application is equipped with features including product search, order status tracking, promotional information and various payment options so that it will better support an electronic-based integrated process to reduce the use of paper and suppresses the increase in CO2 gas.
The application of electronic-based work processes has also been used in warehouse operational management which includes receiving activities, compounding goods, checking, releasing goods, loading onto trucks, cycle counting and stock taking.
Waste generated from manufacturing activities also follows the 3R principles.
The first R, waste reduction, is consistently carried out at each factory location by increasing the efficiency of production processes and equipment which results in reducing the amount of material waste produced by production machines and equipment. The use of plastic packaging in the production process has been gradually reduced by using stainless steel containers that can be reused indefinitely.
The second R, reuse of packaging materials, includes paperboard boxes to transport packaging materials from the packaging factory to the production factory, which are returned to the packaging factory for use under a strict conditions.
The last R, recycling is executed in collaboration with vendors. For packaging materials, such as paperboard boxes, plastic drums, paper drums, etc. that can not be used in Tempo Scan’s production activities and have been strictly evaluated for commercial value, they are sold to reprocessing companies through certified vendors.
Meanwhile, hazardous waste or B3 waste is collected in a licensed temporary storage area, transported and processed further by certified professionals, following the provisions regulated by the environmental authority.
SDG Goal 17: Partnerships For The Goals
The Company establishes mutually beneficial partnerships and respects each other’s rights and obligations with principals, suppliers, vendors and all other stakeholders to achieve the Company goals. One of them is partnerships with external vendors, where in 2023, the Distribution Division has launched TiVEMS®, an integrated vendor management system, to enable partnership management to be carried out more efficiently, optimally and accountably.
As a form of the Company’s partnership with the community in terms of empowering community resources, among others, by employing local workers for activities in the factory area and handing over non-B3 waste processing activities to cooperatives or communities around the Company industry.
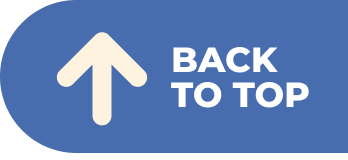